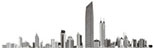
在过去的一百年里,涂料工业已经从科学转向科学。今天,涂料技术使用化学,物理和工程科学。新技术提供新材料,新生产设备,工艺和基材。不幸的是,增长总会带来一定数量的问题。
今天的油漆系统通常非常复杂,我们的技术非常先进,可以忽略问题的确切性质。通常认为问题的原因是化学的,实际上它可能是物理的。
不良色强度或色调以及其他性质(如不透明度,透明度或光泽度)通常归咎于不合格的颜料。许多问题不是由于化学反应或原料质量差,而是由于粒度分布。
以下属性取决于粒度:
可以优化这些性质的程度与所用的分散方法,在固体颗粒上扩展的能量和颜料颗粒经受分散能量的时间长度有关。
絮凝,着色力,色调和透明度。油漆化学家描述了由诸如絮凝等众多机制引起的各种与颜色相关的问题。最常见的例子是用二氧化钛着色的涂料和有色颜料,特别是有机颜料,当施加的湿膜受到额外的能量时会产生更多的颜色。
通常,当白色基底用有机或有色颜料的分散体着色时,会出现这种类型的效果。如果所得混合物由于额外的剪切而显示出颜色变化,通常的结论是有机颜料分散体已经絮凝或由于有机颜料的稳定性方面的化学不足而在白色调基料中絮凝。颜料分散体和白色调基料之间的分散或不相容性。实际上,经常发生摩擦是因为有机颜料颗粒在最初分散时没有充分地解絮凝。有机颜料,如所收到的,处于絮凝状态。高速混合设备没有足够的能量来破碎甚至松散堆积的有机颜料附聚物。因此,如果我们将干燥的,有色的有机颜料添加到白色有色基材中,所得到的面漆不仅会有颗粒感,而且摩擦会表明颜色发展存在巨大差异。摩擦试验虽然是粗糙的,但会使涂层承受相当大的能量,甚至高于高剪切分散体所能达到的能量。
这是一个非常粗糙的例子,我们都知道这些有机颜料必须预分散,以获得理想的结果。然而,我们的许多问题与我们通过将颜料分散体与给定的Hegman研磨读数相关联来鉴定颜料分散体的事实有关。
虽然有用,但是研磨仪的Hegman成色通常会产生误导。Hegman研磨仪仅表示分散体中最大颗粒的大小。它没有表明粒度分布。颜料的抗絮凝状态与粒径有关; 为了获得无摩擦或反絮凝的优秀的结果,颜料必须尽可能接近其最终粒径分散。
对喹吖啶酮紫进行的测试表明,随着颗粒尺寸的减小,当着色白色基底时观察到的摩擦量减少,如图1(右)所示。在图1中,摩擦程度表示在1到10的范围内; 10严重,一个没有摩擦。
色彩强度。为了进一步说明粒径减小对喹吖啶酮紫的影响,分散于7 NS的Hegman细度。这是大多数涂料化学家和生产人员如果想要涂上具有7 NS的Hegman研磨剂的珐琅质就会停止的点; 并且还涉及7 3 / 4 NS,或几乎关闭计。然后用这两种分散体对白色珐琅着色,并进行摩擦,着色强度和色调的比较。由此得到的比较表明,7 NS分散体显着摩擦,并且着色强度也降低了15%。
透明度和色调。当在透明薄膜中比较这些相同的两种分散体时,观察到透明度和色调的巨大差异。制作金属涂层时,这些差异非常重要。当这两种分散体用于制作金属漆面时,结果是显着的。与7NS分散体制备的涂料呈现金属触发器差,无光泽,带蓝色的洗出膜和低光泽度大于与7所作的涂料3 / 4的分散体。
透明薄膜的显微照片显示出粒度分布的明显差异。另外,使用Coulter计数器的实际粒度分布示出了7 NS分散体的平均粒径为6微米,而7 3 / 4样本为0.5微米。
大多数有机颜料在色调,色调强度和透明度方面经历这些显着变化的事实并不是一个新概念。许多涂料制造商牺牲了额外的强度,以避免运行更长的研磨周期或购买更好的设备,而没有意识到放弃10%的强度可能是昂贵的。而且,牺牲了最终产品的最终质量。除非颜料颗粒减小到接近其最终尺寸,否则不能实现金属中的摩擦,透明度,透明度和亮度以及其他性能。
隐藏。正如透明度取决于粒径减小一样,遮盖力取决于粒径。但是,在隐藏的情况下,必须将粒径控制在给定范围内。
二氧化钛被特别加工成0.20至0.35微米的颗粒尺寸,或约等于光波长的一半。通过将该颜料分散到其优秀的尺寸,可以获得最终的遮盖力。还有其他无机颜料在设计上是不透明的。通常,粒径越细,可能的不透明度越高。
无机颜料制造商已经改善了合成氧化物颜料的分散性,使得它们现在促进许多颜料的搅拌或易分散,这意味着可以用高速分散设备实现Hegman 6 NS或更好。虽然这确实是正确的,但通常会牺牲隐藏权力。
通常,这些颜料是红色和黄色氧化物。为了说明上的隐藏粒径,的影响几种氧化物颜料的使用既高速分散到6+ NS赫格曼(25微米)和小介质研磨至7分散1 / 2 NS赫格曼(6微米或更小)。在大多数情况下,当颗粒尺寸减小到合成颜料晶体的近似平均尺寸时,注意到遮盖力的增加。当比较结果时,发现为了达到相等的遮盖力,需要多达15%的颜料,分散剂研磨至仅6 + NS。
当黄色氧化物进一步分散时,发生显着的色移,导致更脏的颜色和遮盖力的损失。严重变色表明原始颜料颗粒破裂或破坏。
当合成氧化铁颜料分散到6 1 / 2 NS赫格曼(20微米),得到预期的暗红色氧化物或栗色样阴影。然而,在进一步分散这些等级时,不仅隐藏能力有明显改善,而且质量色调和色调都转变为中红色氧化铁色调。显着的色调偏移是由于单个颜料晶体的破坏,除了在这种情况下颜料颗粒已经减小到下一个更精细的红色氧化铁生产阶段的尺寸。
虽然还有其他参数有助于遮盖力,但控制粒径不仅会产生优秀的的遮盖力,而且还会因不希望的颜色漂移而减少昂贵的再加工。
消光。在贸易销售以及许多工业涂料中,使用各种添加剂来控制光泽。这些材料包括透明涂料或清漆中的二氧化硅和其他增量颜料,如着色体系中的粘土,滑石和碳酸盐。虽然众所周知,给定涂层中的固体颗粒或颜料的直径必须小于预期涂层的干燥薄膜厚度,但许多人没有意识到当使用二氧化硅降低光泽度时,精确的颗粒尺寸控制是重要的。
据报道,一批缎面清漆的光泽度是10单位光泽度太高; 并且,在添加二氧化硅来校正它之后,15个单位的光泽度太高了?
表I-玻璃速率和粒度 | |
二氧化硅颗粒尺寸,以微米计 | 清漆的光泽 |
35 | 20 |
25 | 三十 |
16 | 42 |
6 | 60 |
原因在于,在二氧化硅中研磨时,系统中已经存在的二氧化硅是地上的,导致平整效率的损失。表I显示了几种组成完全相同的清漆的光泽度,不同之处在于二氧化硅 - 平整添加剂分散到不同的粒度。
平整,透明度和光泽都取决于散射反射光。一旦平整添加剂减少超过给定的粒度,膜表面变得更均匀。这允许更多反射光的入射角等于反射角; 因此,光泽度上升。
光泽。由于减小颗粒尺寸会降低压平效率,因此很自然地认为它有利于光泽。涂层中颜料的粒径会影响薄膜的光滑度并引起光的散射(图3)。
早些时候,分散到不同粒度范围的两种Quin-acridone Violet分散体显示出产生颜色亮度的差异。另外,具有较大粒径的紫色颜料的那些导致约10个光泽单位较低。当试图生产喷射黑色的masstone光泽涂料时,所得涂料的黑度取决于实现最终的粒度分布,特别是因为最黑的炭黑可能具有所有颜料中最小的颗粒(约0.07微米)。
电影外观。更细的颗粒尺寸将产生更好的透明度和光泽度,部分原因在于薄膜的光滑度。在许多涂料,特别是工业涂料中,使用各种蜡,聚乙烯和其它特殊硬聚合物赋予固化薄膜某些性能。这些特性包括较低的摩擦系数, 改善的耐擦伤性和耐磨性以及减少的金属标记。这可以在不对其他性能产生不利影响的情况下实现,例如重涂性,粘附性,光泽度或缩孔率。由于这些材料通过到达固化膜的表面起作用,因此它们的许多有益和不利影响取决于粒度。
由于这些颗粒的作用在膜的表面,显然颗粒越大,对膜均匀性的影响越大。在烘烤涂层中尤其如此,其中这些颗粒在烘烤循环期间变为液体。在它们的熔融状态下,它们通常与涂层的树脂和/或载体系统不相容。因此,膜的平滑度受两种液体的表面张力差异的影响。
图3(右图)显示了在成膜的各个阶段中含有大聚乙烯颗粒的涂层中发生的情况。在涂覆之后并且在烘烤之前,表面附近的固体聚乙烯颗粒产生轻微的膜平滑性破坏并且通过排水使其上方的漆膜壁变薄。
在烘烤过程中,聚乙烯熔化并变成液体。由于表面张力的差异,聚乙烯将使涂料液体从聚乙烯液滴中挤出,形成凹坑。在干燥和冷却后,聚乙烯液滴回复到固体,并且在经历一些收缩的同时,保持为球状。
当然,颗粒越大,陨石坑越大。这会影响透明涂层的薄膜完整性,透明度和光泽度,以及着色涂层中的反射图像。通常,这可以通过减小粒度来控制,这不仅减少了膜的缺陷,而且还增加了所用添加剂的活性。
流变性和稳定性。油漆生产通常使用预分散的颜料浓缩物,无论是在室内生产还是从外部供应商处购买。因为这些浓缩物用于各种化学上不同的涂层,所以天然需要广泛的相容性。
为了达到这种效果,这些浓缩物的制造商试图使配方尽可能简单,以防止由于使用不必要的添加剂而产生的不利影响。另外,这些色母料通常长时间保存在库存中,因此必须显示出良好的储存稳定性。
许多油漆化学家认为有时候应该使用添加剂以防万一。一个例子是流变改性剂或增稠剂和抗沉降剂。通常这是在没有清楚地了解添加剂是否真的必要的情况下完成的; 其他方法来达到要求的结果; 或者对老化有什么不良影响。
对于预分散的色母料,需要两种类型的稳定性:1)耐老化稳定性; 2)老化时抗絮凝性。
在引入可能对耐水性,宽范围相容性,絮凝,流动和流平等性质产生不利影响的添加剂之前,应评估的第一个参数是作为粒度函数的分散稳定性。
通过以下三种方式减小粒度来改善颜料分散的稳定性:
流变学和/或粘度。减少颜料粒径会增加颜料表面积,这通常会导致粘度增加。而且,许多有机和甚至无机颜料体系都具有触变状态。较高的粘度或诱导的触变性可防止颜料流动,防止沉降和再絮凝。
预防絮凝。在絮凝中,颜料颗粒倾向于再附聚,导致颜色强度损失和颜色均匀性差。减小颗粒尺寸将防止再附聚。减小粒径会增加系统的粘度; 它进一步降低了迁移的可能性。
沉降。大多数涂料制造商的主要稳定性问题之一是解决问题。颗粒尺寸的差异可以在液体介质中沉降球形物体时显示出广泛变化的结果,并将其应用于分散体或涂层体系中颜料颗粒的速率或沉降。由于简单的粒径减小,我们可以看到稳定性获得的值。
粉化,耐光性和耐候性。除了包装稳定性之外,固化膜的稳定性或涂布和固化后涂层的性能可受颜料粒度的影响。
不透明涂料需要各种颜料,这取决于它们的选择,会影响涂料性能。在许多情况下,颜料的选择基于美学或经济价值,并且很少考虑其与所需涂层性质或粒度对这些性质的影响的实际性质。
对于边缘性质的体系,粉化,耐光性和光泽保持性可能受到粒度减小的不利影响。用通用级二氧化钛与分散到不同粒度范围的合成红色氧化铁和黄色氧化铁颜料组合进行的简单实验导致耐水性,光泽保持性和粉化的显着差异。一些边界颜料的耐光性也同样受到粒度分布差异的影响。
为了显示这些效果中的一些,制备基于完全相同的载体类型和颜料比的釉质并将其分散到不同的粒度范围内。在一种情况下,颜料由2:1比例的二氧化钛和黄色氧化铁组成; 在另一种情况下,二氧化钛和红色氧化铁的比例为2:1。
以两种颜色制备涂料,其平均粒度范围为25微米和6微米。如所预期的,更细的粒度在未曝光的板中产生更高的光泽度。如表II所示,500小时的QUV暴露导致表观光泽和颜色变化
表II-QUV暴露结果 | ||||
黄色氧化物/ TiO 2 | 红色氧化物/ TiO 2 | |||
25μ | 6μ | 25μ | 6μ | |
光泽(未曝光) | 91 | 94 | 92 | 94 |
光泽(暴露) | 70 | 52 | 72 | 53 |
曝光时光泽度下降 | 21 | 42 | 20 | 41 |
曝光损失的强度% | 3.5 | 7 | 4 | 7 |
E暴露 | 1.43 | 1.85 | 1.05 | 1.45 |
粒径的减小导致颜料表面积的增加。因此,颜料减少到6微米的涂层将有更多的颜料暴露在表面上,具有较少的载体以防止变质。由于二氧化钛的粉化速度比铁氧化物快,因此老化时强度明显下降。在洗涤曝光区域并将其与未曝光区域进行比较后,结果显示两个表面具有相同的光泽度和颜色,表明上述数值结果的变化严格地归因于粉化。这些结果是通过使用通常预期会发白的颜料组合获得的。选择对粉化更具抵抗力或对光不太敏感的颜料会降低所示的效果。然而,
具有更细粒度分布范围的涂料显示出明显更好的耐水性。其原因可以解释为,在这些实验中,颜料组合是有意地选自那些可能是亲水性最强的颜料。在图4(右图)中,其示意性地表示包含不同粒度的两种涂层,我们可以看到较大的粒度倾向于提供芯吸效应,水分可以通过该芯吸效应传播到基底。这导致涂层的起泡,软化和最终破坏以及金属基材的腐蚀。尽管我们已经在聚合物技术方面取得了优秀的技术,为我们提供了能够美化,保护,隔离甚至与给定基材反应的涂料